The realities of climate change have driven another big year in material innovation in 2024. Here are 10 of the best solutions that have put a promising spin on cement, plastic, fur, linoleum, or even introduced something new.
For many designers and engineers experimenting with materials, the drive has been to replace high-emissions building materials as quickly and practicably as possible, with concrete regularly spotlighted for contributing as much as eight per cent of carbon emissions globally.
Others are targeting plastic, whether by replacing it with plant-based alternatives or taking different approaches to biodegradability and recycling.
Read on for 10 of the standout material innovations of this year:
Aquafade water-soluble plastic by Pentaform
Pentaform is a tech start-up focused on making gadgets from a type of plastic that dissolves in water, leaving behind only the electronic components for easy recycling.
The product – for instance, a computer or remote control – is given a thin waterproof coating on the outside to protect it from moisture, but when its housing is opened and the whole thing is submerged in water, it completely dissolves in six to eight hours.
The idea is that the plastic-water mixture is tipped down the sink or toilet so it can finish decomposing in the sewage system – a readily accessible watery composting facility.
Find out more about Aquafade ›
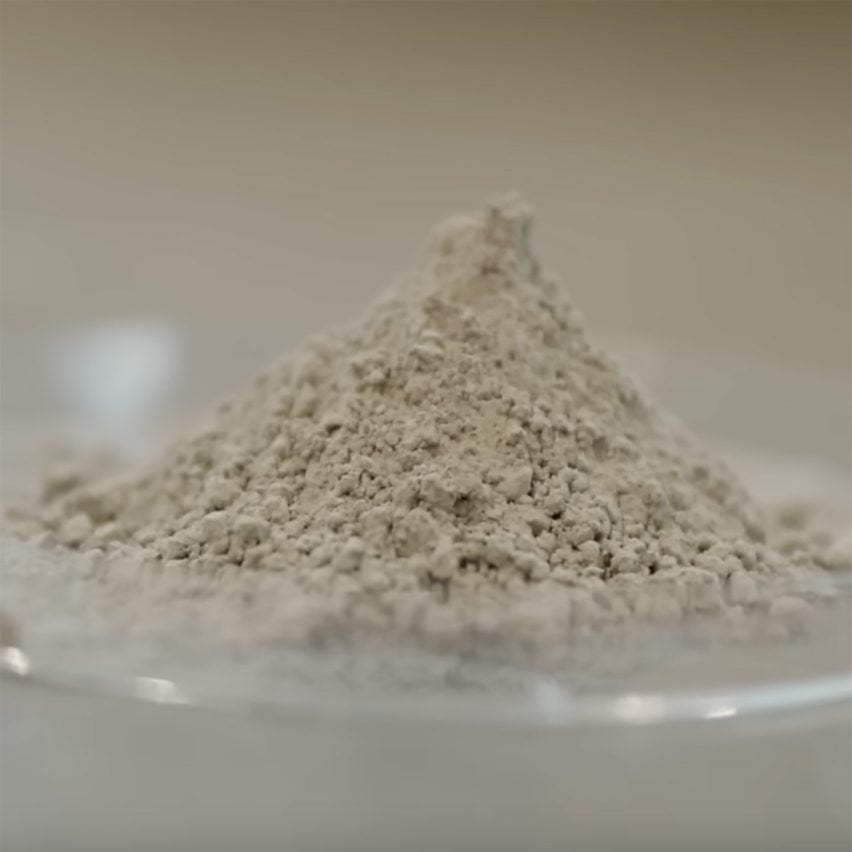
Recycled cement by Cambridge Electric Cement
There’s a lot of competition in the race to produce a zero-emissions concrete to meet the world’s construction needs, but one of the most promising in terms of how quickly it could be scaled up and brought to market is this solution from researchers at the University of Cambridge.
The method involves recycling old cement from demolished buildings by heating it up and reactivating the compounds within it. However, the key is how this process is executed: by piggybacking off the existing electric-powered furnaces used to recycle steel, where the cement is used in place of standard lime “flux” to purify metal.
This addresses both of the major sources of cement’s high emissions: the chemical reaction as limestone is turned into new cement, and the firing of fuels to power the high-heat kilns needed for that process.
Find out more about recycled cement ›
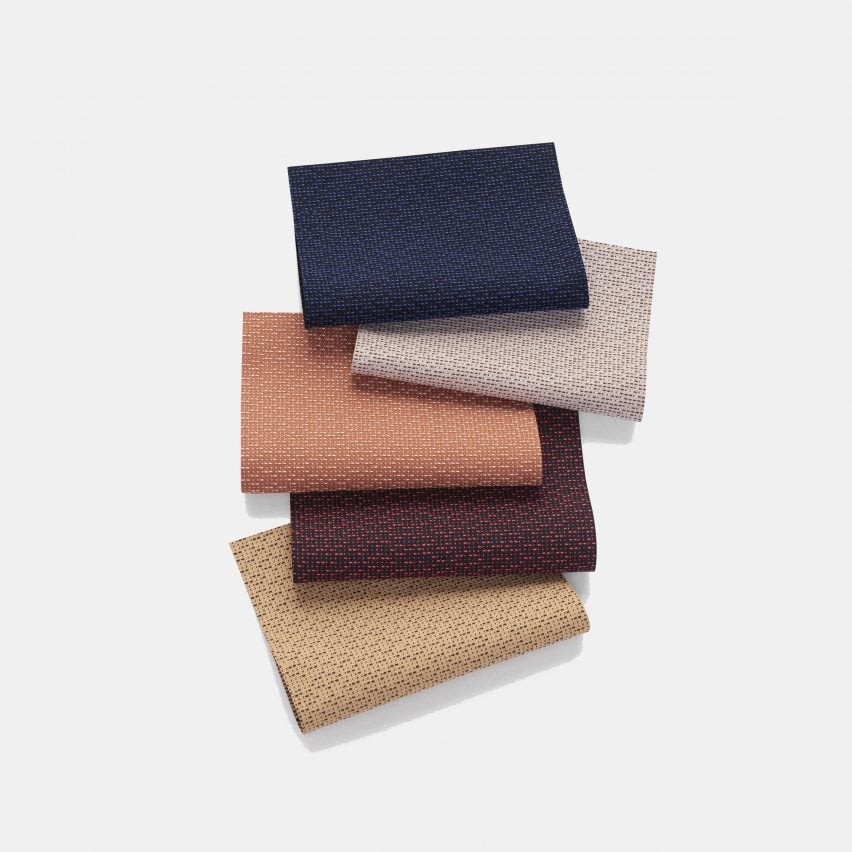
Ame by Kvadrat
Not everyone realises it, but fabrics that are marketed as recycled polyester are usually made from plastic bottles and other kinds of PET packaging, and not waste polyester textiles of the same kind.
One of the first textile-to-textile recycled polyesters is Kvadrat’s Ame, which was developed with designer Teruhiro Yanagihara.
To create it, the company used chemical recycling, a group of technologies that is considered controversial. But the upside of this approach is that it can keep textiles within a closed loop and stop the death spiral of downcycling.
Find out more about Ame ›
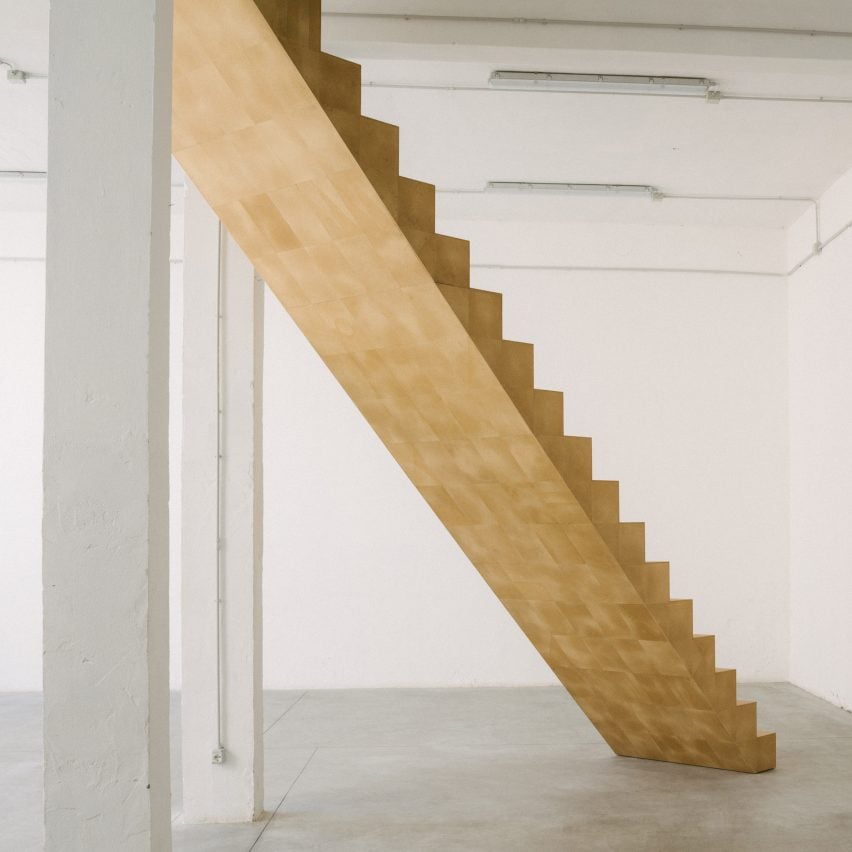
Flaxwood tiles by Christien Meindertsma and Dzek
Sometimes the innovation is not in making something new but making us rethink something old. Christien Meindertsma aimed to rebrand linoleum and establish a new visual language for the misunderstood material with the Flaxwood tiles she created for manufacturer Dzek.
Unlike plastic-based vinyl and PVC, linoleum can be made entirely from renewable and reclaimed materials – typically linseed oil, pine resin, wood dust and chalk – and is biodegradable and endlessly remouldable.
In Flaxwood, all the pigments, coatings and backings that normally disguise its natural composition are stripped away to reveal a warm honey colour and mottled texture. The hope is that the work can help to reframe linoleum as a material of the future rather than just a holdover from the 1970s, which it is often perceived as.
Find out more about Flaxwood ›
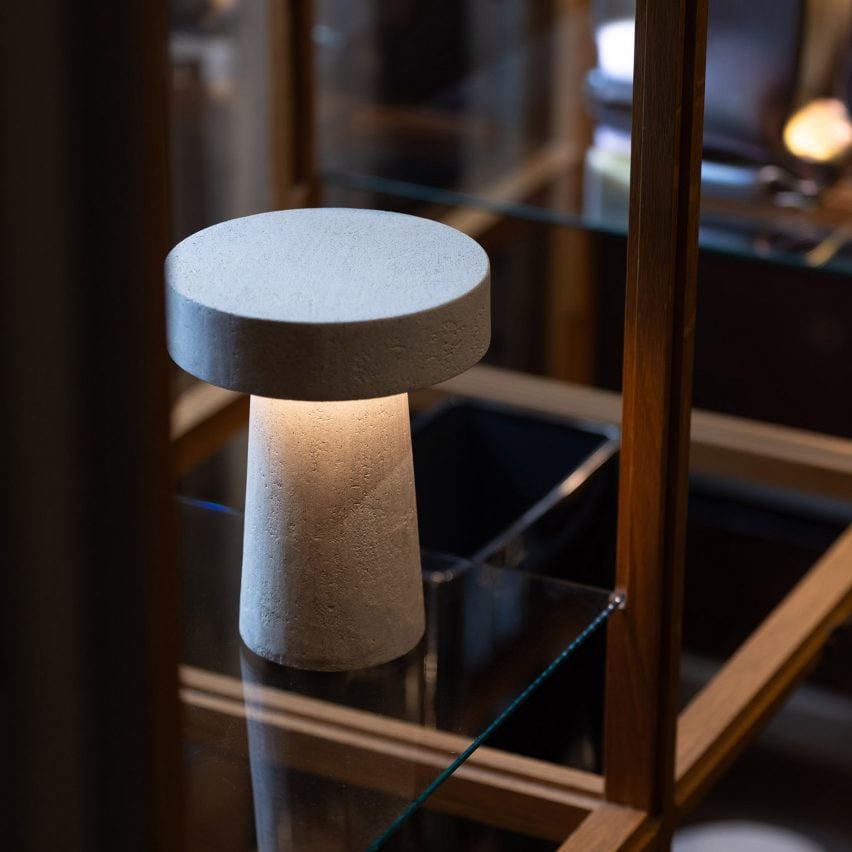
Remli lamp by We+
The Remli lamp is made from We+’s Remains material, a composite containing a mix of urban detritus that the studio describes as “hardly recyclable”.
The waste, gathered from construction sites around Tokyo, is ground into a powder, with molten glass acting as a binder to create a material with a finish similar to concrete.
“Remli reimagines waste materials from Tokyo as new vernacular materials,” said We+.
Find out more about Remli ›
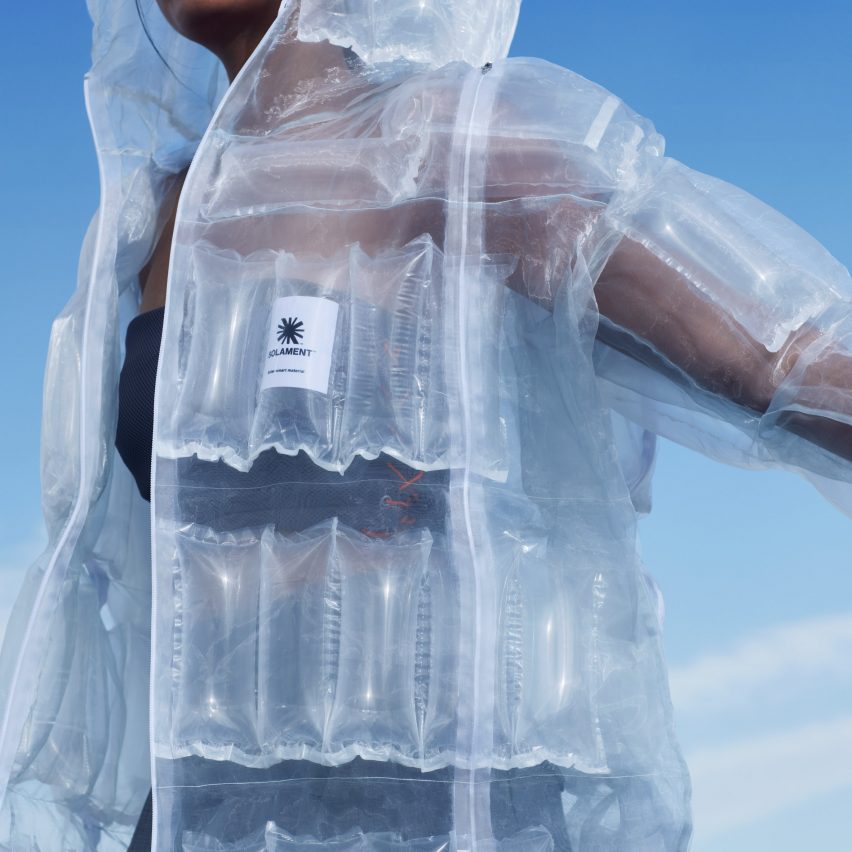
The Down-Less Down Jacket by Sumitomo Metal Mining Co
Sumitomo Metal Mining Co collaborated with consultant Droga5 Tokyo and fashion designer Kosuke Tsumura to create the Down-Less Down Jacket as a way of demonstrating the potential of its heat-producing Solament material.
The material utilises a particle developed by Sumitomo called CWO to absorb near-infrared light, which is invisible to the human eye, and convert it into heat, warming the body “instantly”.
The material can also be used to block heat, and the company believes it could have multiple applications – for example on automobile windows.
Find out more about the Down-Less Down Jacket ›
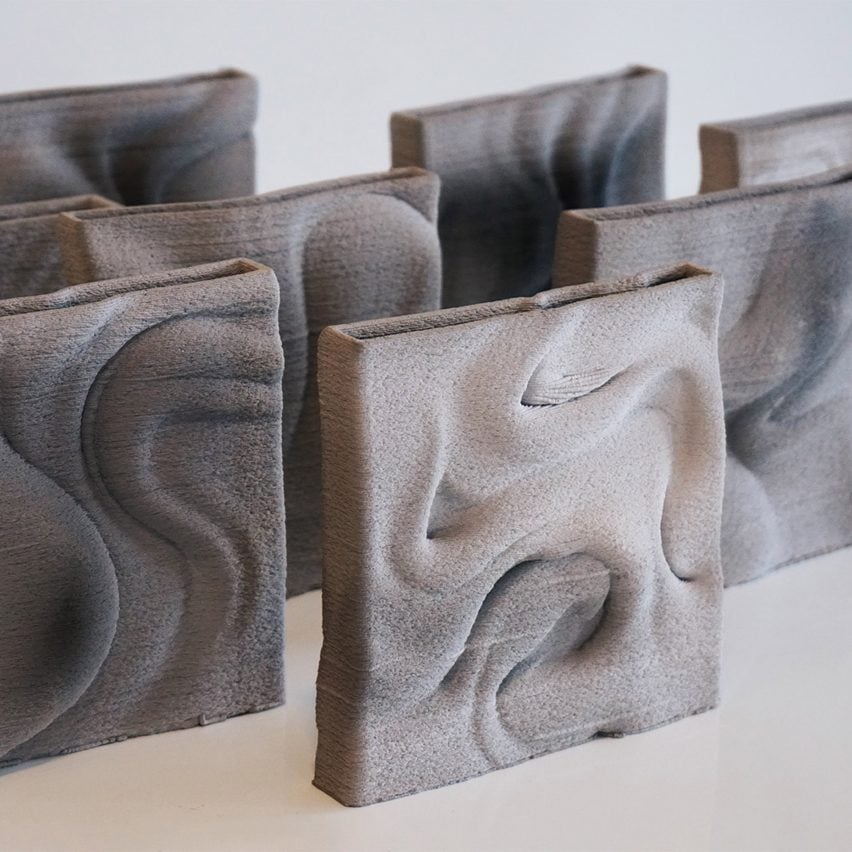
RePit by Nawa
One of the challenges with biomaterials is how to create them using sources that are abundant and won’t put further strain on the environment. Enter Omani design collective Nawa with RePit, a plastic-free filament for 3D printing made from waste date pits.
The pits are crushed and mixed with natural Omani clay and palm fibres to make an iteration of a traditional water-resistant lime mortar known as sarooj.
Nawa has made a series of decorative tiles with this material, which represents one way of making use of the nearly one million tonnes of date pits produced by the global date industry each year.
Find out more about RePit ›
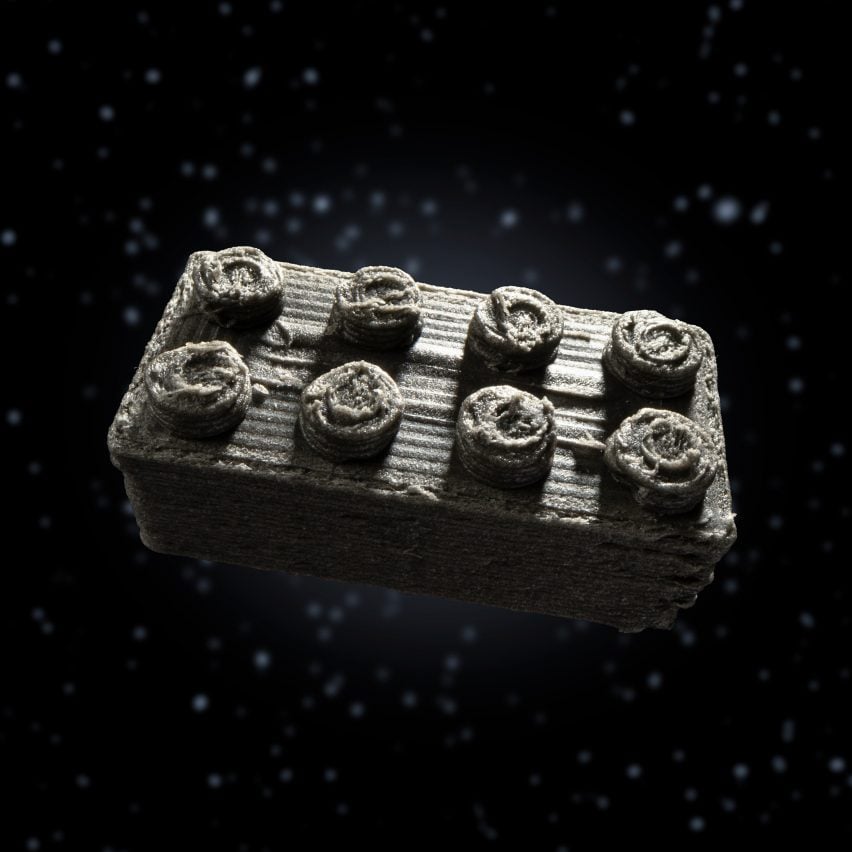
Space bricks by Lego and the European Space Agency
Transporting materials from Earth to the moon is prohibitively expensive, so space agencies are energetically exploring possible ways of building structures using lunar regolith.
Using meteorite dust as a substitute, the European Space Agency (ESA) 3D printed its own version of a Lego brick capable of being locked together like the famous toy building blocks.
“Our teams are working towards the future of space travel and take inspiration from not just what’s above us, but also what we can find on Earth,” said ESA science officer Aidan Cowley.
Find out more about space bricks ›
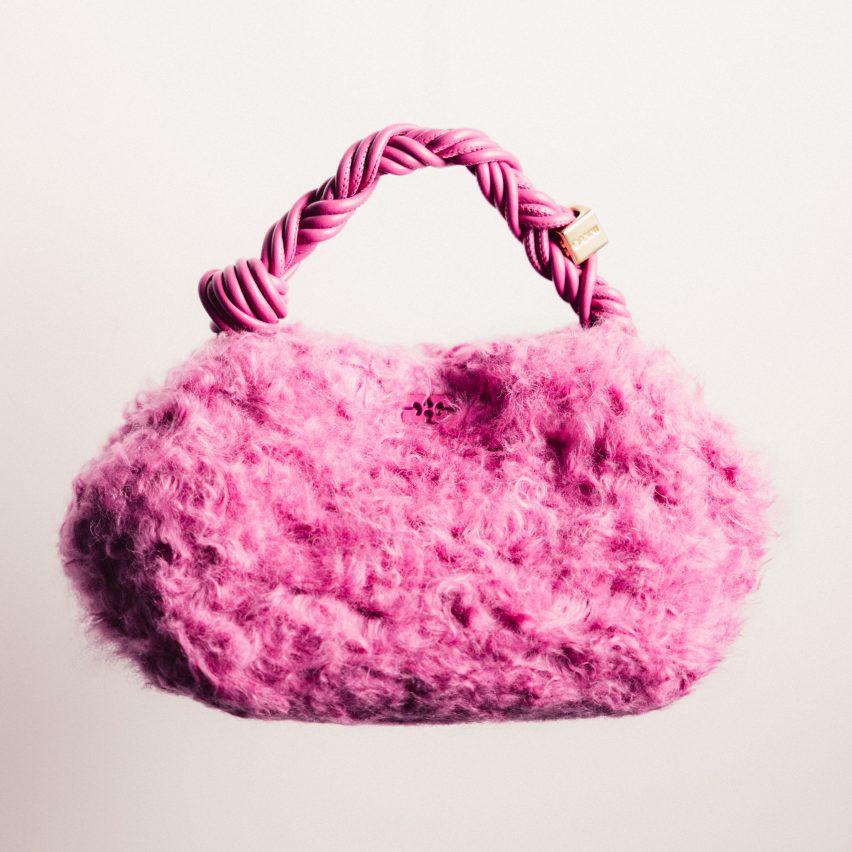
Biofluff bag by Ganni
This one-off version of Ganni’s Bou bag is made from a material by the start-up Biofluff, which claims to have developed the world’s first plant-based fur.
Unlike existing faux furs, the shaggy textile contains zero plastics or petrochemicals, according to the manufacturer. Instead, its hairy fibres are extracted from plants and agricultural waste using special enzymes that are also plant-derived.
As well as a faux fur, Biofluff makes a plant-based plush material for children’s toys.
Find out more about Biofluff ›
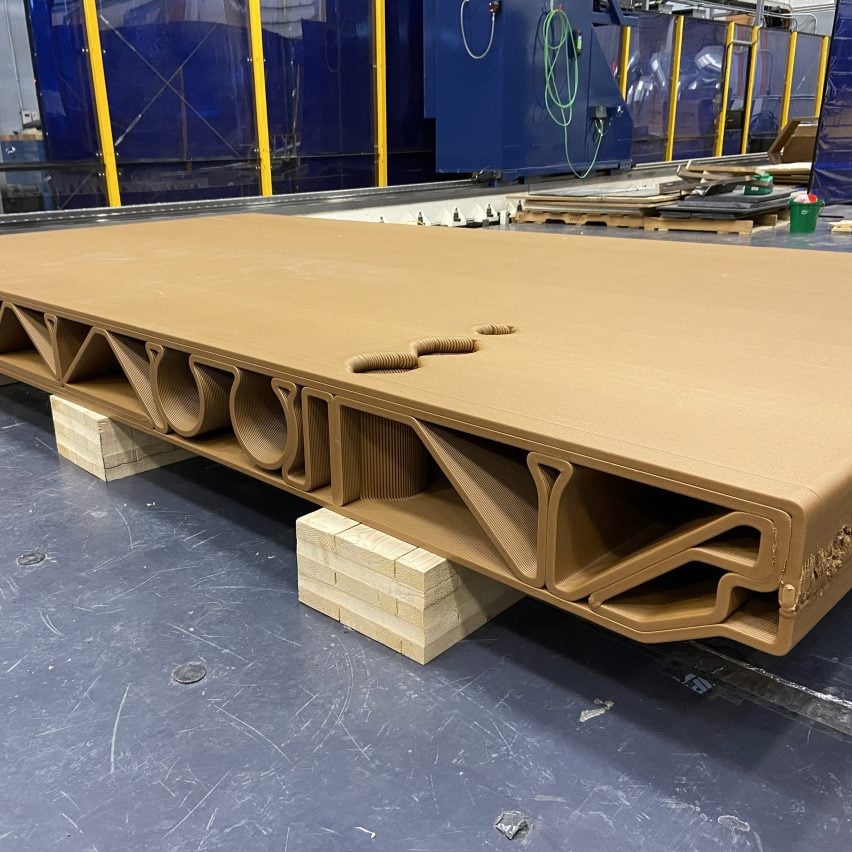
SM2ART Nfloor cassette panel by Oak Ridge National Laboratory and the University of Maine
A material innovation for the largest scale of human construction, the SM2ART Nfloor cassette panel is made of a mix of wood waste and bioplastic.
Thanks to the material properties and the shape it’s 3D printed in, it is strong enough to be used in place of conventional steel and concrete floor cassettes in high-rise buildings.
According to the research team behind it, it is also quicker to make and easier to recycle.
Find out more about the SM2ART Nfloor cassette panel ›